Overview of 3D Printing in Car Manufacturing
3D printing has transformed car manufacturing by offering unparalleled customization and efficiency. This technology enables on-demand production, reducing waste and speeding up delivery times.
Evolution of 3D Printing Technologies
Additive manufacturing, the foundation of 3D printing, dates back to the 1980s. Initially, industries used it for prototyping, not mass production.
In recent years, advancements like;
- Stereolithography (SLA)
- Selective Laser Sintering (SLS)
have emerged. SLA uses UV lasers to solidify liquid resin, creating detailed prototypes.
SLS employs a laser to fuse powdered material, producing durable parts. These developments have made 3D printing viable for manufacturing complex car components.
Benefits of 3D Printing in Automotive Production
3D printing offers several benefits in automotive production.
- Reduced Lead Times: On-demand printing lessens the gap between design and production.
- Cost Savings: Custom parts cut down on manufacturing waste, decreasing costs.
- Design Flexibility: Complex geometries become achievable, promoting innovation.
- Sustainability: Fewer resources are wasted, contributing to eco-friendly production.
These efficiencies indicate why car manufacturers increasingly adopt 3D printing for various components, from engine parts to custom interiors.
Key Areas Impacted by 3D Printing
3D printing significantly affects various aspects of car manufacturing. From prototype development to producing spare parts, it revolutionizes how vehicles are made.
Prototype Development
3D printing accelerates prototype development. Traditional methods take weeks or months, but 3D printing reduces this to days. Rapid prototyping allows car manufacturers to test multiple design iterations quickly.
For instance, I read that Ford uses 3D printing to develop prototypes of new car models, which cuts down time and cost significantly. Engineers can refine designs efficiently, leading to faster innovation cycles.
Customization and Personalization
Customization reaches new heights with 3D printing. Manufacturers can tailor parts to individual customer preferences without incurring high costs.
Personalized interiors, custom-fit components, and unique design elements become feasible. For example, BMW offers bespoke interior features produced through 3D printing, enhancing customer satisfaction.
This tool enables automakers to provide a unique experience for each customer, reflecting personal tastes and requirements.
Spare Parts Manufacturing
Spare parts manufacturing becomes more efficient with 3D printing. Traditional inventory systems can be costly and time-consuming, but 3D printing allows on-demand production of parts.
This reduces the need for extensive stockpiles. Volkswagen uses 3D printing for producing rare spare parts for classic cars, ensuring availability without maintaining large inventories.
It ensures that even older models have parts readily accessible, improving vehicle longevity and customer service.
Case Studies: Automakers Using 3D Printing
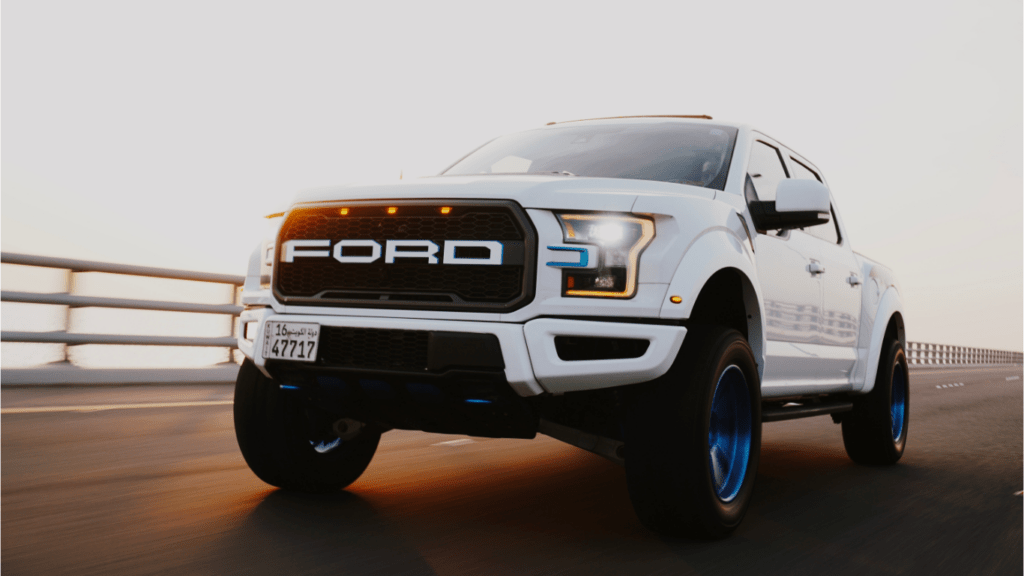
Several automakers have adopted 3D printing to innovate and streamline their manufacturing processes. Here are key examples:
Ford and Volkswagen Innovations
Ford uses 3D printing to produce customized brake components.
This cuts production time from weeks to days. Ford also integrates 3D printing into its assembly line to create tools, jigs, and fixtures, resulting in significant cost savings.
Volkswagen employs 3D printing for producing rare spare parts for classic vehicles. By using HP’s Multi Jet Fusion technology, it rapidly produces components like wing mirrors and gear knobs, ensuring high precision and durability.
The automaker also explores incorporating 3D-printed titanium parts for future models to reduce vehicle weight and enhance performance.
Local Motors and the Strati
Local Motors revolutionized car manufacturing by producing the world’s first 3D-printed car, the Strati. Using Direct Digital Manufacturing (DDM), it printed the vehicle’s body in approximately 44 hours.
The Strati comprises just 49 parts, compared to thousands in conventional cars, showcasing 3D printing’s potential for simplification.
The Strati’s production process uniquely combines 3D-printed parts with traditional automotive components like electric motors and suspension.
This hybrid approach underscores the practical integration of 3D printing in mainstream car manufacturing.
Advancements and Future Trends
3D printing continues to transform the automotive industry, pushing the boundaries of what’s possible in manufacturing processes and product design.
Emerging advancements and future trends indicate even more revolutionary changes on the horizon.
Materials and Technology Innovations
Material advancements drive 3D printing forward. Car manufacturers now use high-performance polymers, carbon-fiber composites, and titanium alloys.
These materials provide durability, strength, and lightweight characteristics essential for automotive applications.
Technology innovations include Multi Jet Fusion and Direct Metal Laser Sintering. Multi Jet Fusion produces parts with excellent detail and accuracy, making it suitable for complex components.
Direct Metal Laser Sintering allows printing with metals, facilitating the creation of robust and heat-resistant parts like engine components.
Predictions for the Automotive Industry
Experts predict several trends in the automotive industry owing to 3D printing. The growing adoption of additive manufacturing for end-use parts will likely increase.
As materials and processes improve, more critical vehicle components will be 3D-printed.
Customization will become more prevalent. Car buyers could select bespoke features, leading to personalized vehicles.
Additionally, on-demand manufacturing might revolutionize supply chains, reducing the need for large inventories and enabling rapid production of spare parts.
These advancements and trends indicate a future where 3D printing plays a central role in car manufacturing, fundamentally changing how vehicles are designed, produced, and customized.